Step 1. Refining Process
The ‘refining process’ involves adding and mixing various chemicals to crude rubber according to the characteristics and intended use of each tire. Rubber sheets are created by adding plasticity to rubber so that its shape does not change easily.
Step 2. Extrusion Process
Once rubber sheets are made according to the characteristics of each part of the tire through the ‘refining process,’ rubber is then created into a certain regular width and thickness through the ‘extrusion process.’ Here, the treads (outer surface of the tire) and sidewalls (sides of the tire) are created, which is an important process for cozy and comfortable driving.
Step 3. Rolling Process
The ‘rolling process’ involves evenly applying and thinly topping a certain thickness of rubber sheets created in the ‘refining process’ on both sides of steel cords and fabric cords. Rubber is coated on the front and back by pushing steel cords and fabric cords through the constantly rolling rollers. Tires can endure the car weight and maintain a certain form due to this ‘rolling process’ (cords).
Step 4. Bead Process
The ‘bead process’ is the process of coating steel wires with rubber multiple times in a certain thickness, and attaching filler rubber here. Beads fix the rubber of the tires to the wheels, serving as the frame of tire rims and thus making the tires stronger if there are more beads.
Step 5. Molding Process
Now, there is the ‘molding process’ in which cylindrical green tires are made by consecutively attaching all components and materials used in tires to the molding press. This ‘molding process’ requires a great of attention since it determines the quality of the tires. Radial tires used in automobiles first require the process of attaching the ‘carcass’ (the frame of the tire located inside the tread), ‘beads’ (the frame fixed on the rim of wheels), and ‘sidewalls.’ Then, they are transferred to the secondary molding press to complete tires by attaching belts and treads.
Step 6. Curing Process
The ‘curing process’ involves adding heat and pressure inside and outside by putting tires made of flexible rubber in a fixed mold. Sulfur and other chemicals react to rubber and create a unique design of ROADSTONE on the tread, and also apply elasticity to the rubber. Also, they provide any desired structure, shape, exterior, and mechanical/chemical characteristics.
Step 7. Test Process and Shipping
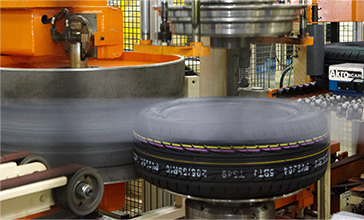
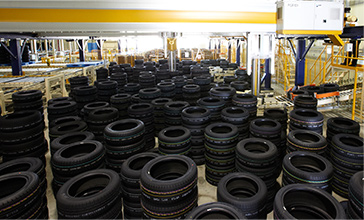
The ‘test process’ consists of five detailed tests.
First, there is the ‘visual test’ that inspects the exterior and interior of the tire as well as the bead with the naked eye. Second, there is the testing of the tire as a single product before assembling on the wheel, and also whether the tire weight distribution is consistent in the circumferential direction (*direction of ultrasonic beam that is vertical to the main shaft of the cylindrical device) in the static state. Third, there is the ‘dynamic balance test’ that measures the weight uniformity in the circumferential direction after rotation when the tires are assembled on the wheels and optimal air pressure is put into the tires. Fourth, there is the ‘uniformity test’ that tests the uniformity of size and rigidity of the product. Finally, x-rays are used to test the carcass inside the tires, structure of belts, and mixing of foreign matters, after which the manufactured products are automatically classified and shipped.